
For the purpose of this discussion, I shall call these items a 'hex key' which goes into the 'hex hole.' I don't know what the proper terminology is for these parts, it's all a bit confusing. Let's keep it simple: hex key goes into hex hole. (update: I'm actually using a high quality hex bit, which is driven by 3/8" drive)
So, normally one holds the strut shaft with a hex bit (or hex key) while using a 17mm wrench to spin the top nut free. Unfortunately, the hex key has STRIPPED the hex hole on top of the strut shaft.
When I did the rear, it got stripped too (why????? salty air probably!) but I was able to hammer in a torx bit which held the rear damper strut shaft in place, while I spun the top nut free. This is NOT possible for the front, there is simply no clearance for hammering in anything. There is no clearance for drilling from the top, no clearance for anything except doing it the way it was intended in the factory manual, which is no longer possible because the hex hole is stripped.
So, the only way I can think of to hold the strut shaft in place is to cut the strut boot (we're throwing away all old struts dampers and springs anyway) and possibly drill through the strut shaft creating a hole large enough to stab a philips screwdriver through and using that to hold the strut shaft in place, while I spin the top nut free. Is this likely to work? Googling the issue, some people suggest using a vise grip, or a pipe wrench, but I don't think this can work because the amount of force needed to bite into the shaft and deform it to hold it in place cannot be generated with these tools. I would need some tool to bite into the strut shaft to hold it in place, I can't think of a tool that can generate enough force to deform strut shaft steel.
These pictures are for reference only, it shows someone else's very clean car (same YEAR MAKE MODEL AS MINE) which shouldn't have any issues. You can see the lack of work clearance, there is even less space on the passenger side. For this vehicle design, one cannot remove the whole strut without first removing the top nut. Once it strips....... oh..... boy....


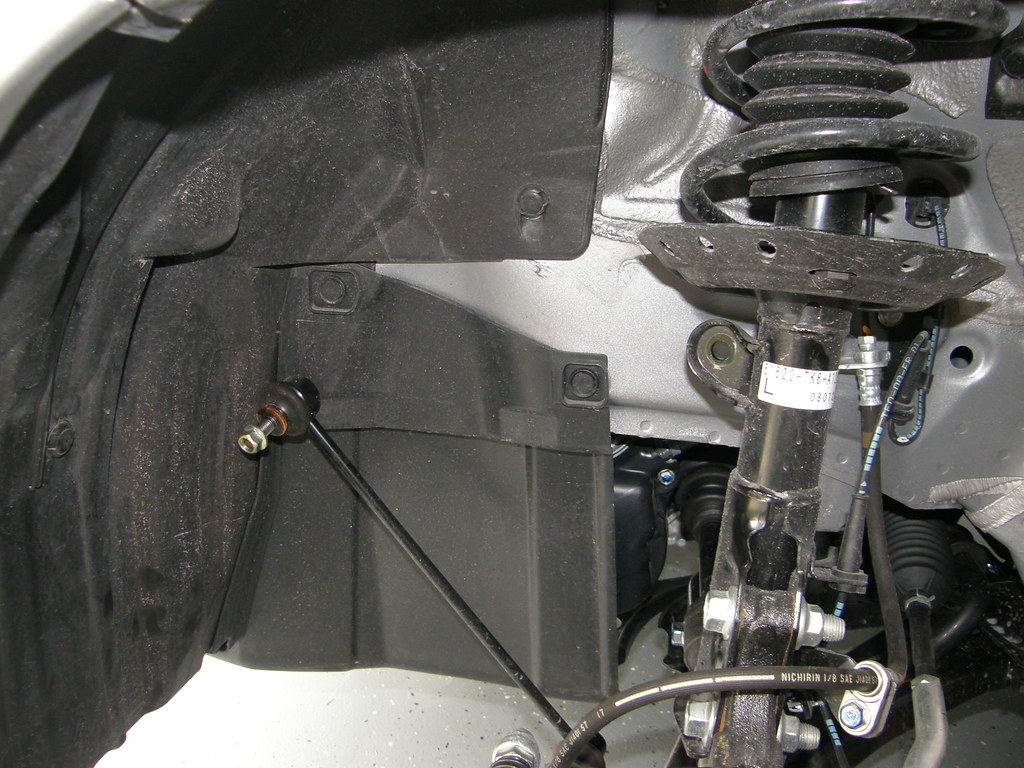
------------------------------------------------------------------------
Do you have some tips to prevent stripping the hex hole for the other side?
-I have already sprayed PB plaster on both sides
-I'm thinking about wrapping the hex bit (3/8" drive) with a layer or two of ALUMINUM FOIL (to reduce play when inserting the hex bit into the hex hole)
(does this make sense?? I've never heard anyone doing it.)
-does it make sense to clean the threads before starting?
-does it make it sense to DESTROY the threads before starting, the idea is to remove as much possible obstruction against the nut spinning out.
Last edited: