JHZR2
Staff member
There are a couple videos on Youtube and maybe some other pictorals, but I asked a lot of questions and went through the learning curve doing my strut job. Thus I wrote up this DIY, which I posted onto the Saab forum I frequent, but wanted to put it here too for anyone who may be inclined to do this job and wants to know how...
I needed to replace a strut bearing on my 2004 9-3 with 72k miles. Ive owned the car since new, and in the last few months, I noted the strut binding when turning to the right. Ive owned the car since new, and it hasnt gotten a ton of use in the last year or so. Ill also note that I did notice that during cold weather, going over bumps, I was getting a crunching sound which I thought was sway bar bushings, but it was the struts!!!
I replaced mine with Bilsteins, which are more expensive than the OE Sachs and aftermarket KYBs, but are IMO a better design. I replaced front struts as well as rear shocks. Ride is much better, and firm but not harsh as others have defined it.
I used a combination of sockets, wrenches, a spring compressor, jack/jackstands, some wood blocks, a flat screwdriver, allen wrenches, female torx sockets, and some Boeshield T-9 and Wurth Film.
The first step is to suitably support the car. I use jack pads from Reverse Logic and JackPoint Jackstands. I did raise the whole front axle, vs just one side and then the next to get it on the stands, but these pads and stands are more stable and easier to use without causing damage.
Once up, youll want to support the rotor/steering knuckle for when you remove the strut. I started with some heavy wood but then decided to use a jackstand on the axle.
Note that my rotors have always rusted nearly instantly. These are original rotors and pads. Pretty good amount of pad left!
The job starts by removing the strut from the steering knuckle. It is two hammered in bolts (they have a funny head and using an impact, I didnt have to hold the head with a wrench), and then two 18mm nuts. Youll also need to remove the brake line and ABS sensors from the bracket on the strut, and the sway bar link on the side of the strut, which uses the same 18mm nut. That sway bar link needs a wrench (17mm) that is very thin to keep the ball joint from spinning. I knocked one boot off by accident due to using a thick wrench.
Be careful!!
When the steering knuckle nuts are off, then use a hammer to knock the bolts to the point where the threaded end is no longer sticking out.
After the items below are removed and the bolts hammered flush, go up top and remove the mount covers (if desired to put them someplace safe). Youll need a star socket to remove the bolts. I used an impact to loosen them, but the torque isnt that great so hand tools are fine, the impact just spun them out faster. I removed two and left one with just a bit of thread.
Next, you can separate the strut from the knuckle, and then move it to a convenient spot.
Supporting the strut from the bottom, then remove the final bolt from up top and pull it out.
The spring rate is indicated by the color marks on the springs.
I needed to replace a strut bearing on my 2004 9-3 with 72k miles. Ive owned the car since new, and in the last few months, I noted the strut binding when turning to the right. Ive owned the car since new, and it hasnt gotten a ton of use in the last year or so. Ill also note that I did notice that during cold weather, going over bumps, I was getting a crunching sound which I thought was sway bar bushings, but it was the struts!!!
I replaced mine with Bilsteins, which are more expensive than the OE Sachs and aftermarket KYBs, but are IMO a better design. I replaced front struts as well as rear shocks. Ride is much better, and firm but not harsh as others have defined it.
I used a combination of sockets, wrenches, a spring compressor, jack/jackstands, some wood blocks, a flat screwdriver, allen wrenches, female torx sockets, and some Boeshield T-9 and Wurth Film.
The first step is to suitably support the car. I use jack pads from Reverse Logic and JackPoint Jackstands. I did raise the whole front axle, vs just one side and then the next to get it on the stands, but these pads and stands are more stable and easier to use without causing damage.
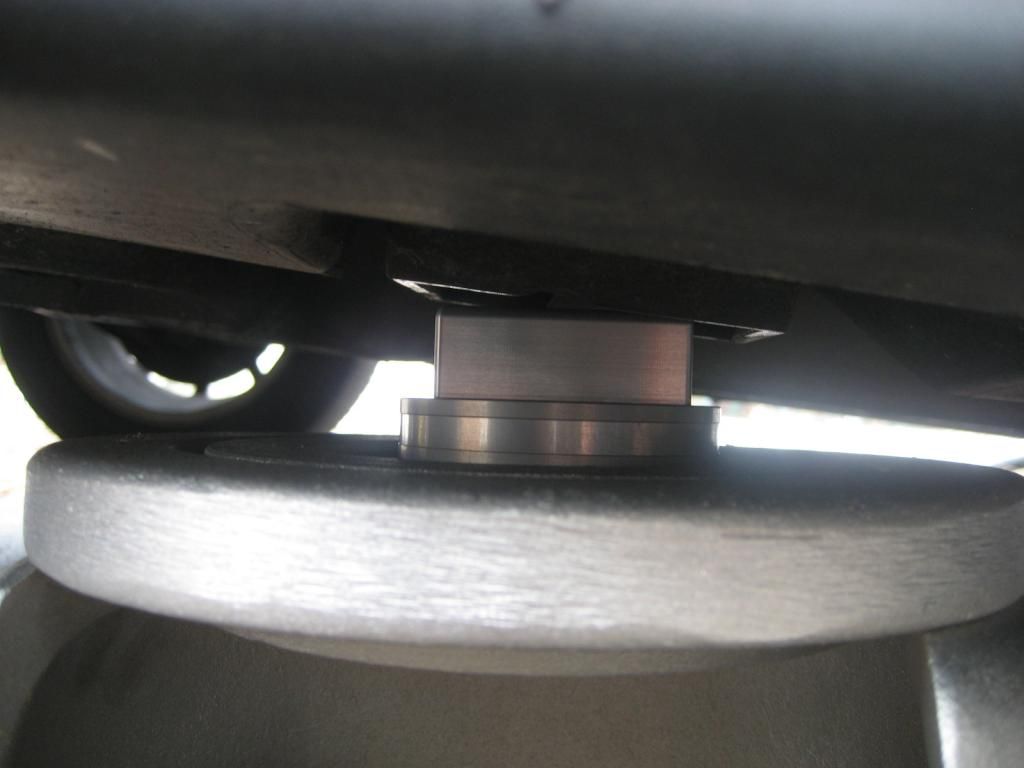
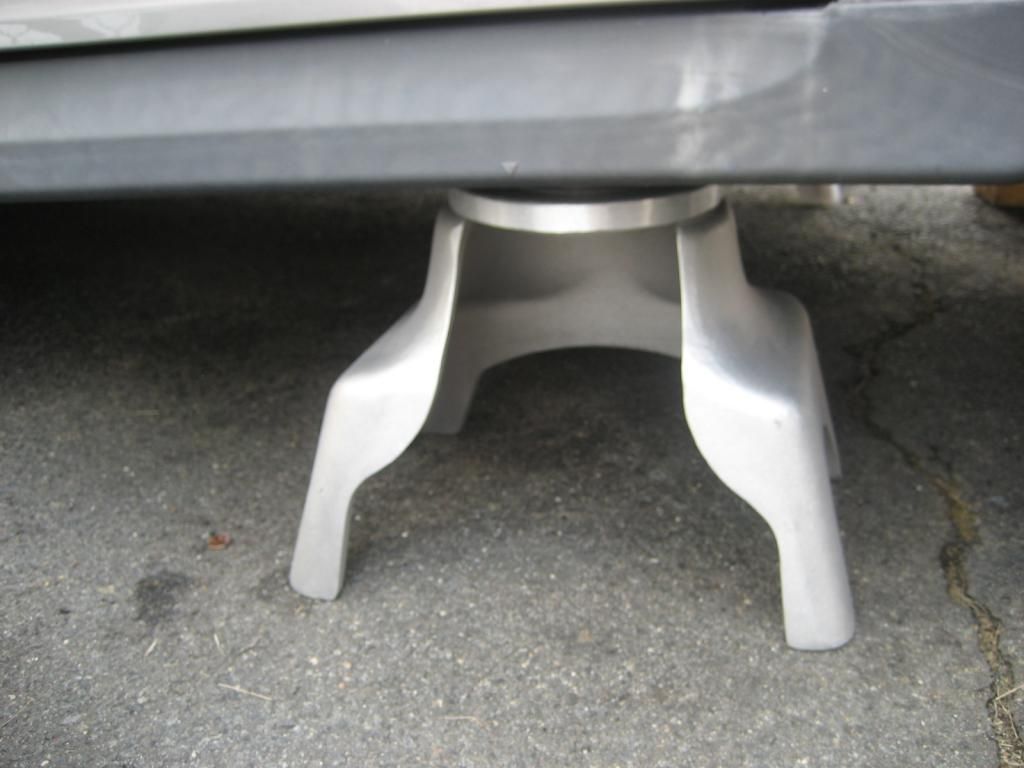
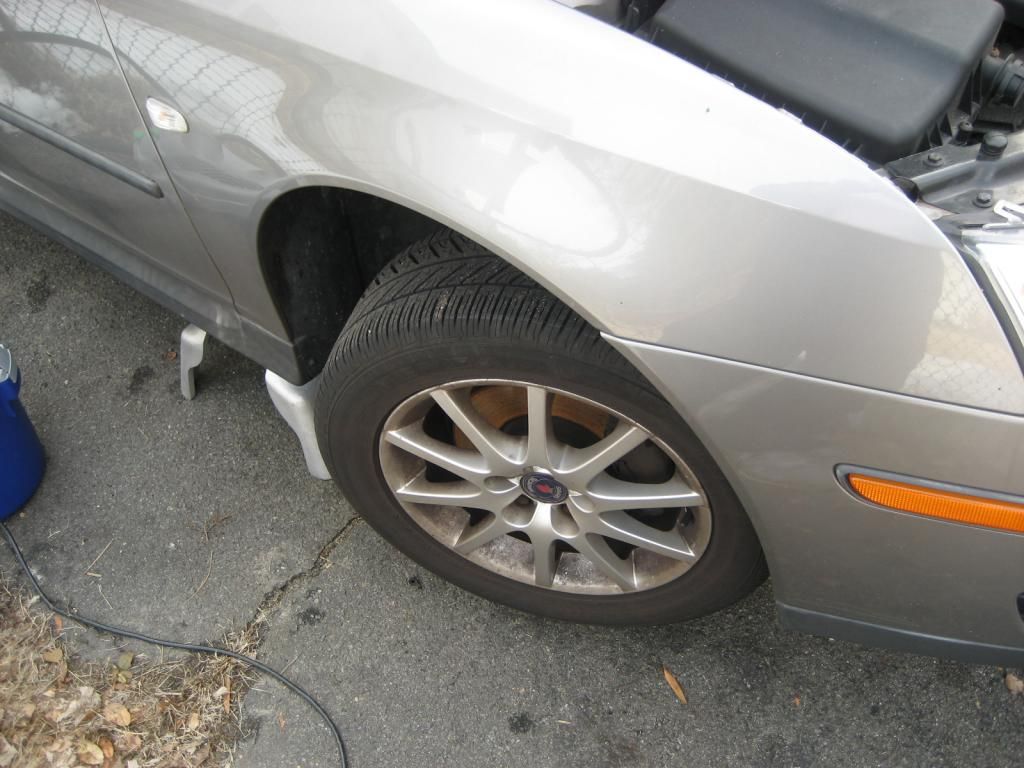
Once up, youll want to support the rotor/steering knuckle for when you remove the strut. I started with some heavy wood but then decided to use a jackstand on the axle.
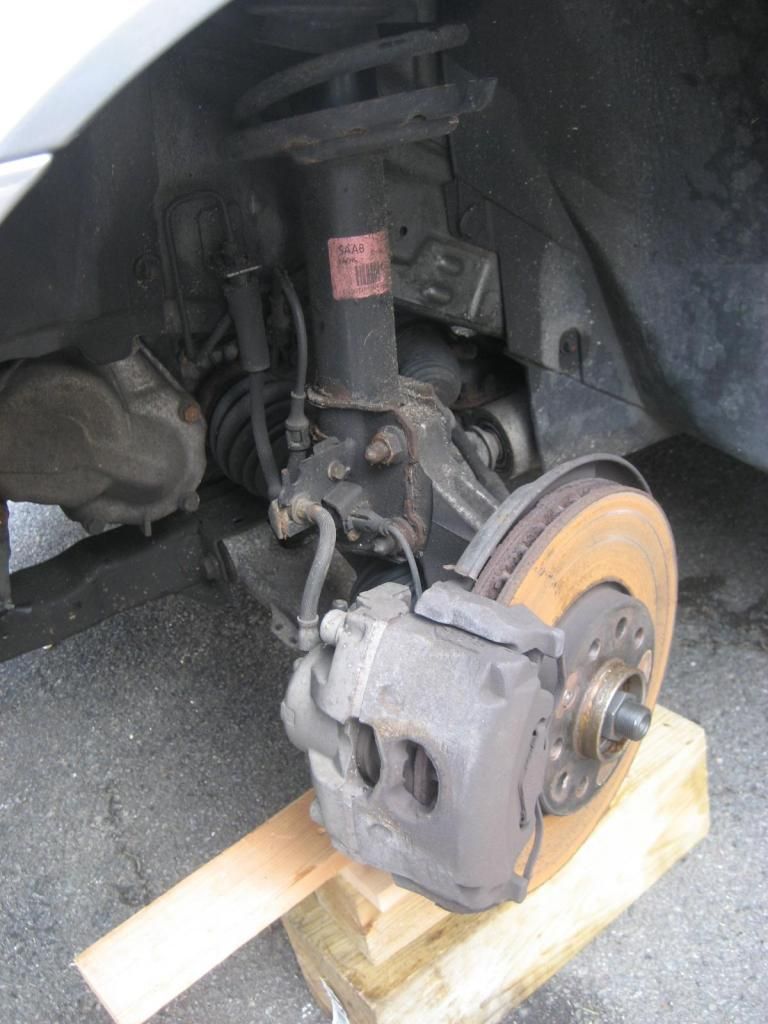
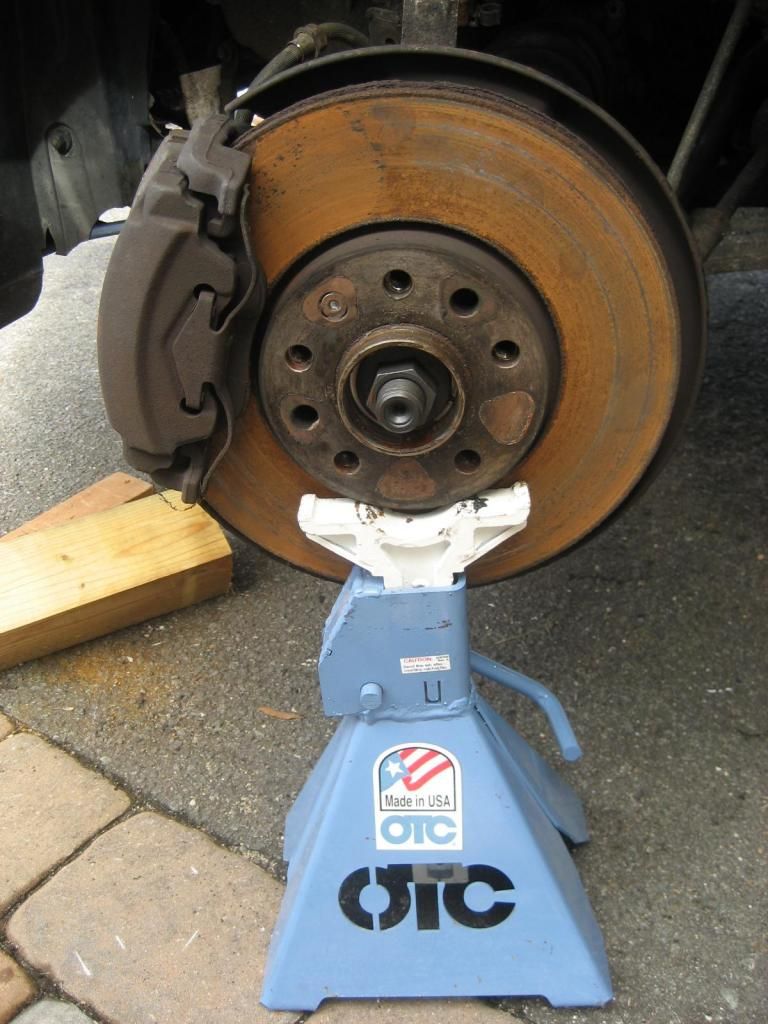
Note that my rotors have always rusted nearly instantly. These are original rotors and pads. Pretty good amount of pad left!
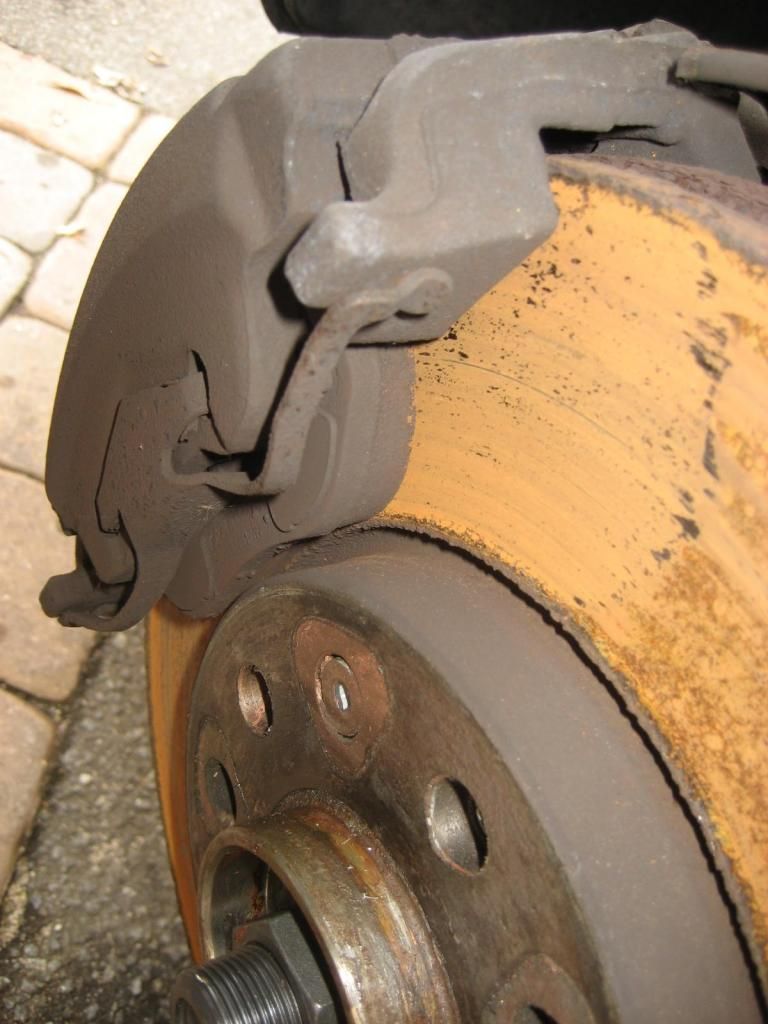
The job starts by removing the strut from the steering knuckle. It is two hammered in bolts (they have a funny head and using an impact, I didnt have to hold the head with a wrench), and then two 18mm nuts. Youll also need to remove the brake line and ABS sensors from the bracket on the strut, and the sway bar link on the side of the strut, which uses the same 18mm nut. That sway bar link needs a wrench (17mm) that is very thin to keep the ball joint from spinning. I knocked one boot off by accident due to using a thick wrench.
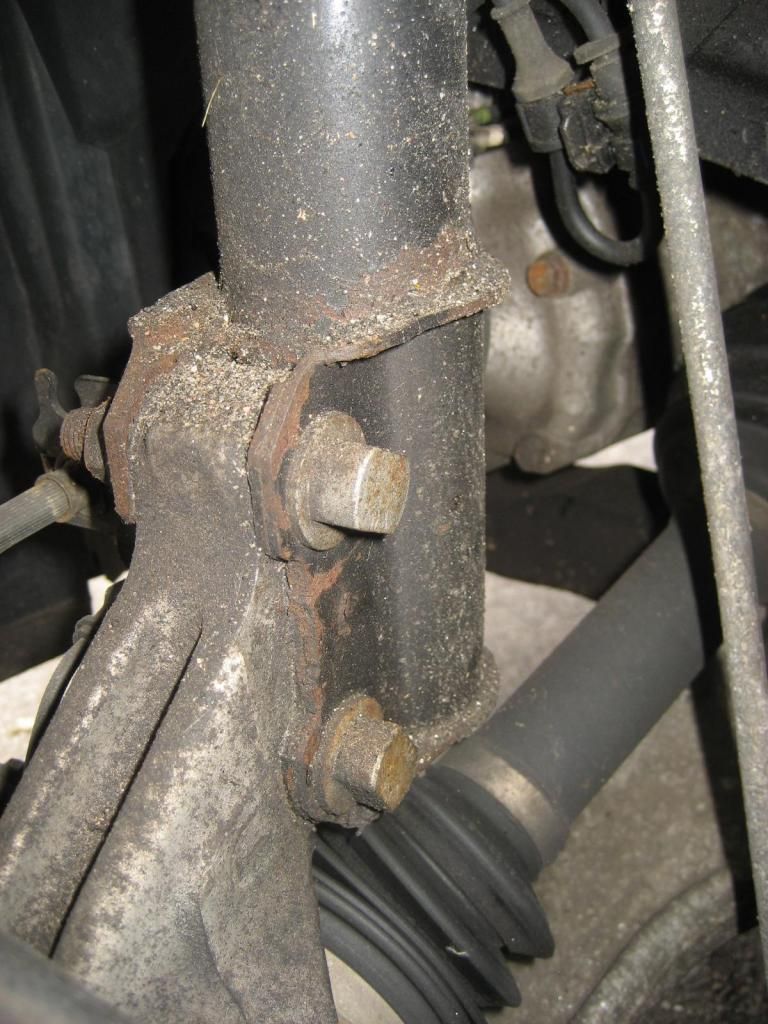
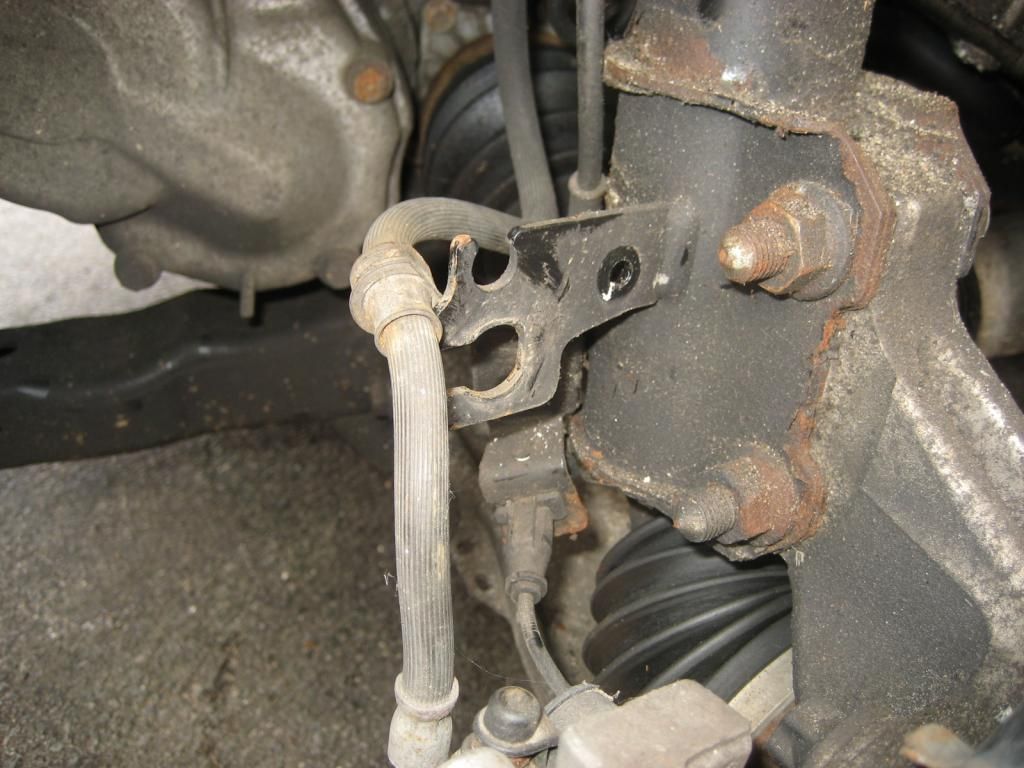
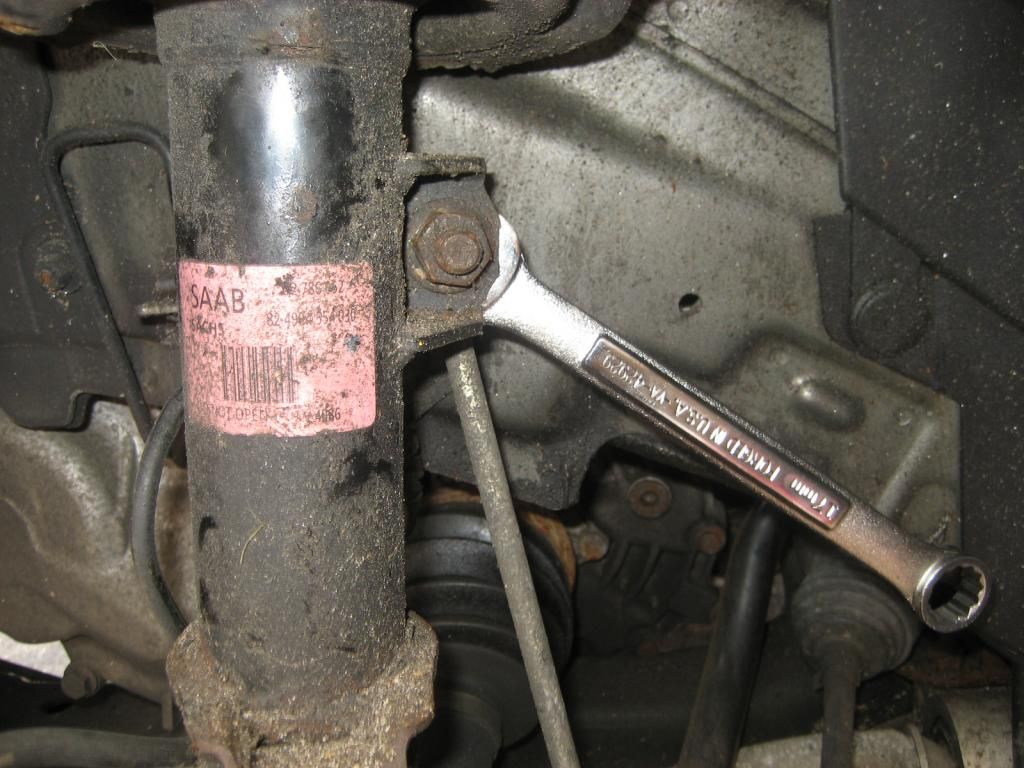
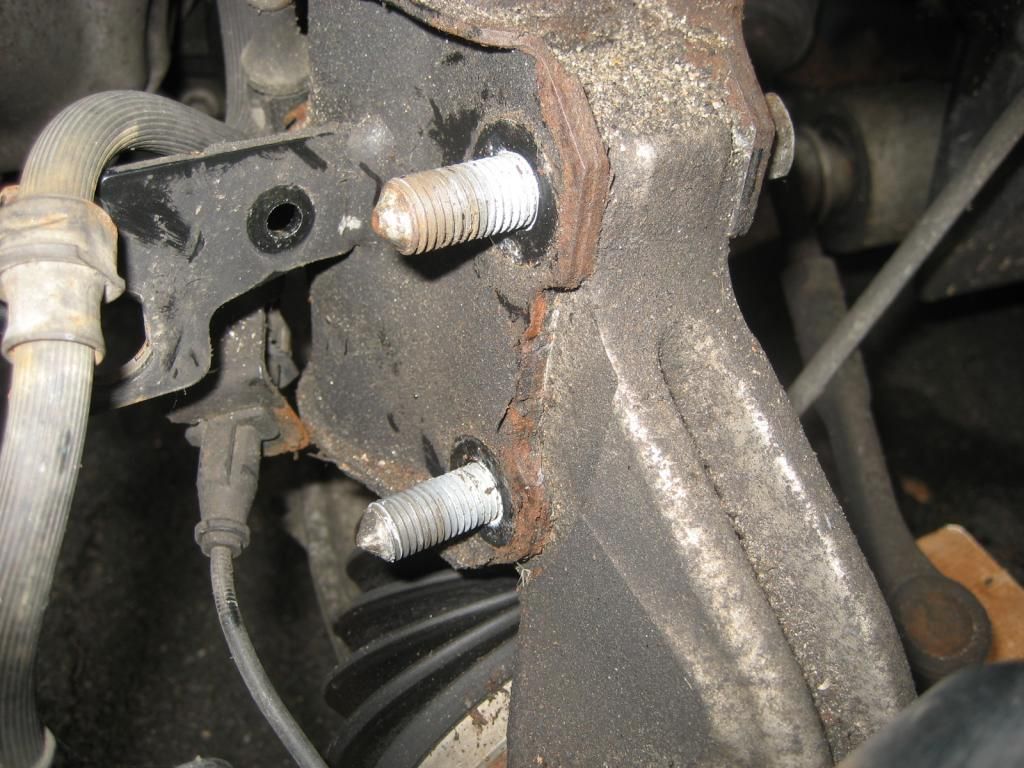
Be careful!!
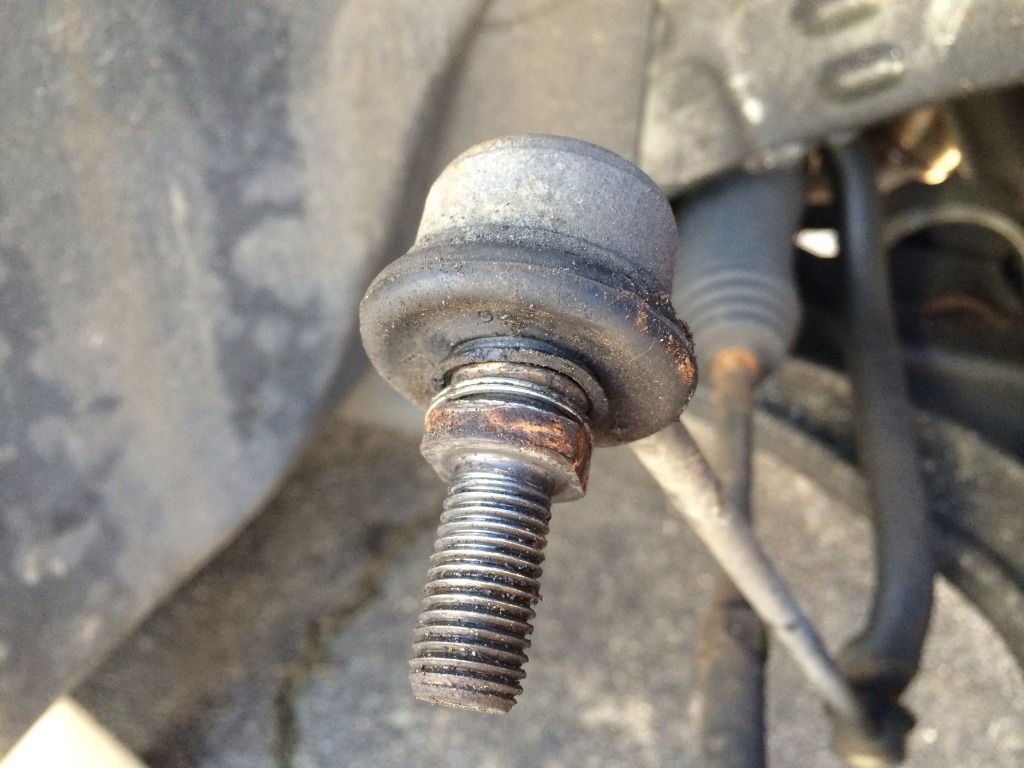
When the steering knuckle nuts are off, then use a hammer to knock the bolts to the point where the threaded end is no longer sticking out.
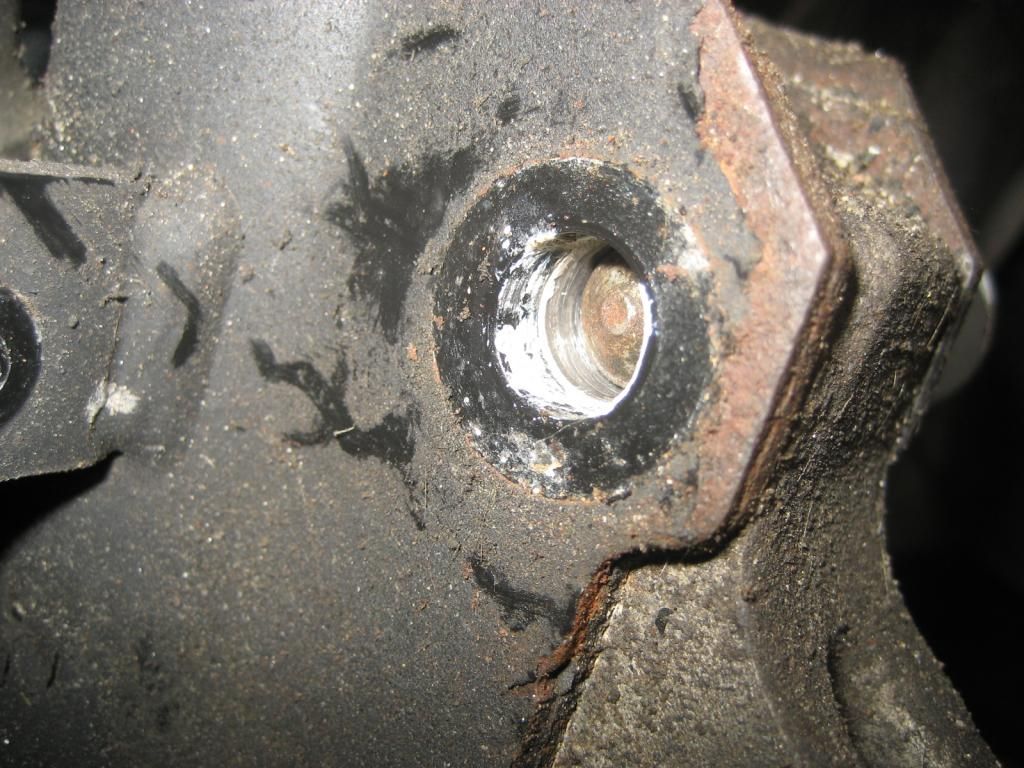
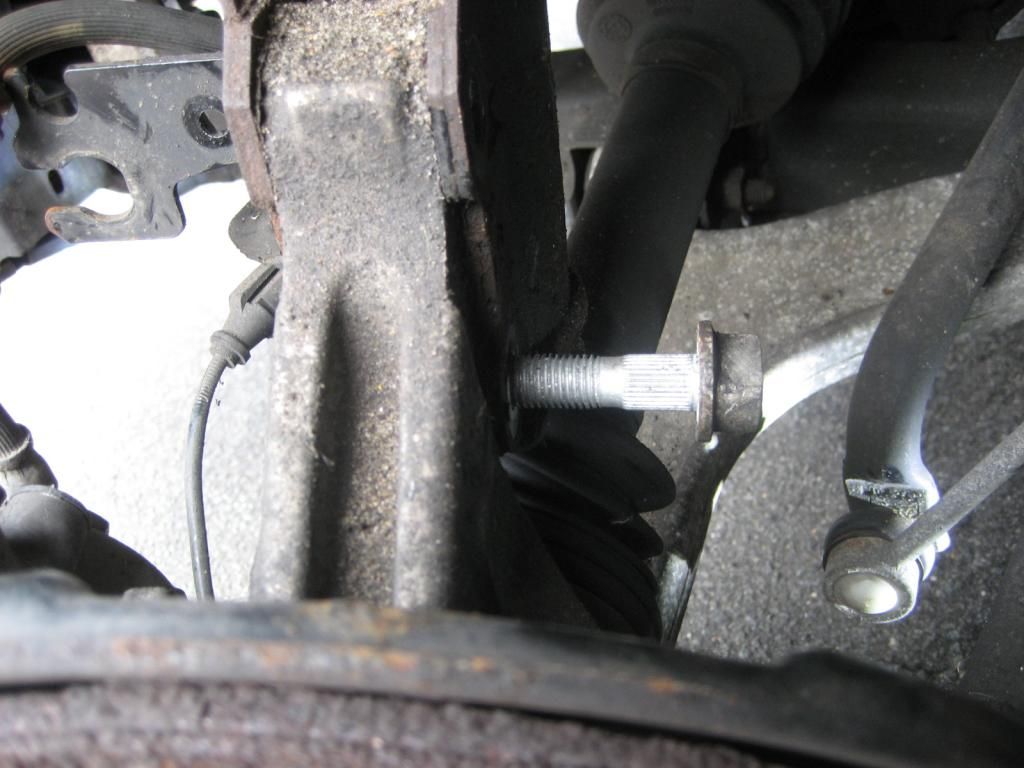
After the items below are removed and the bolts hammered flush, go up top and remove the mount covers (if desired to put them someplace safe). Youll need a star socket to remove the bolts. I used an impact to loosen them, but the torque isnt that great so hand tools are fine, the impact just spun them out faster. I removed two and left one with just a bit of thread.
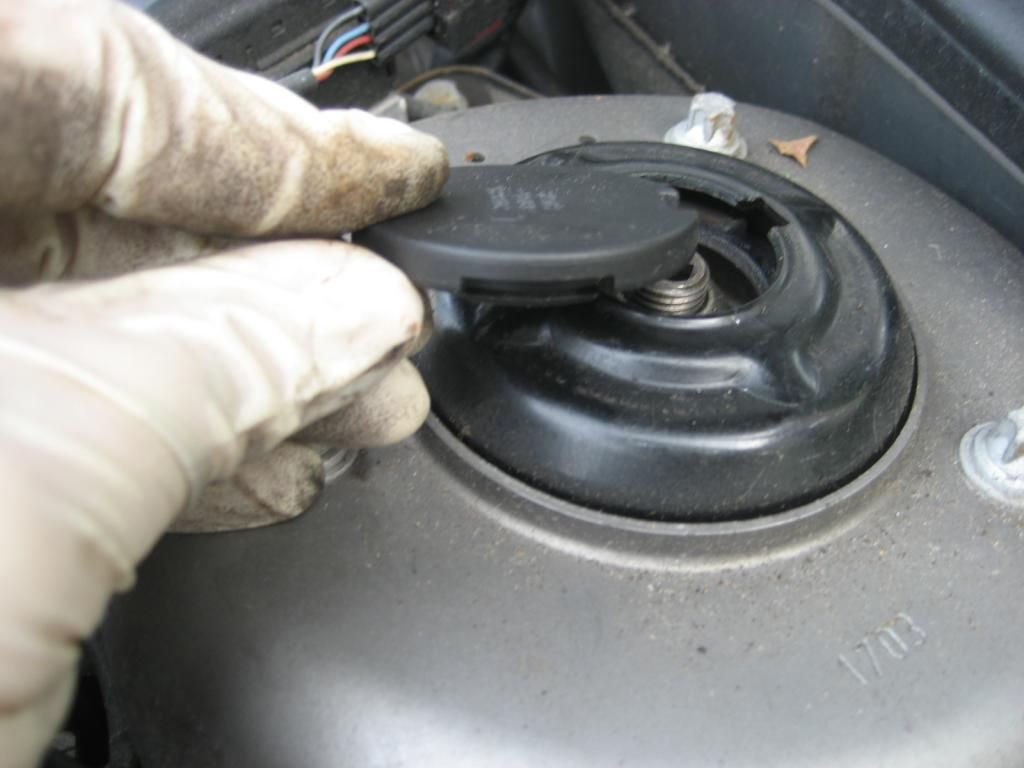
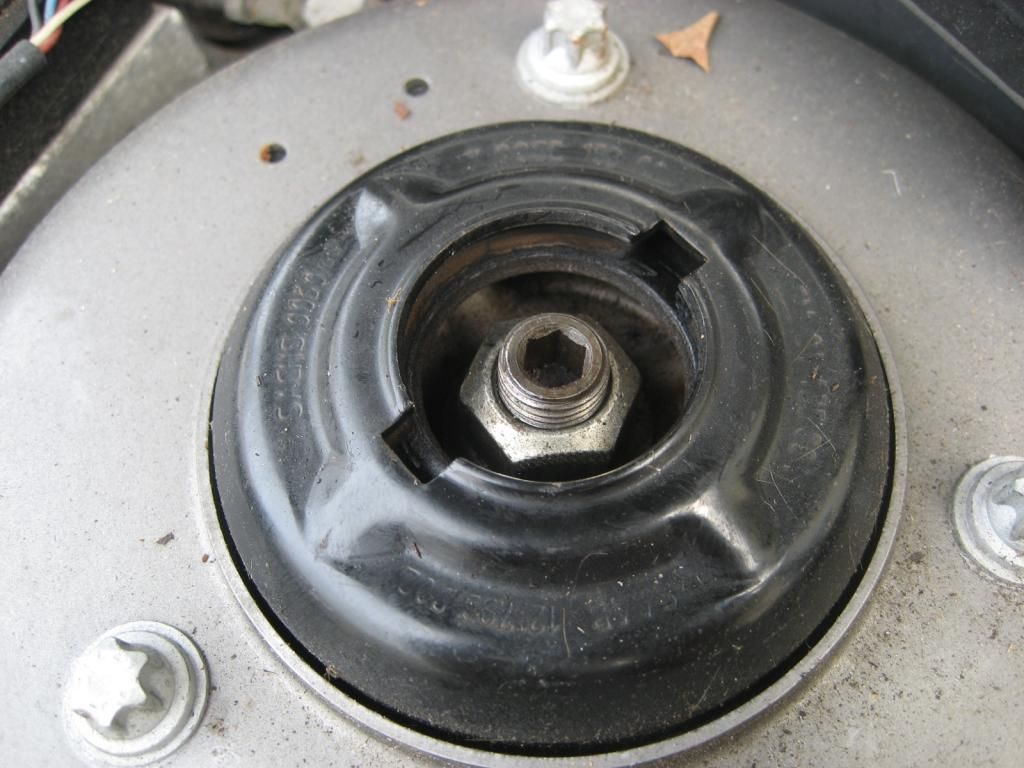
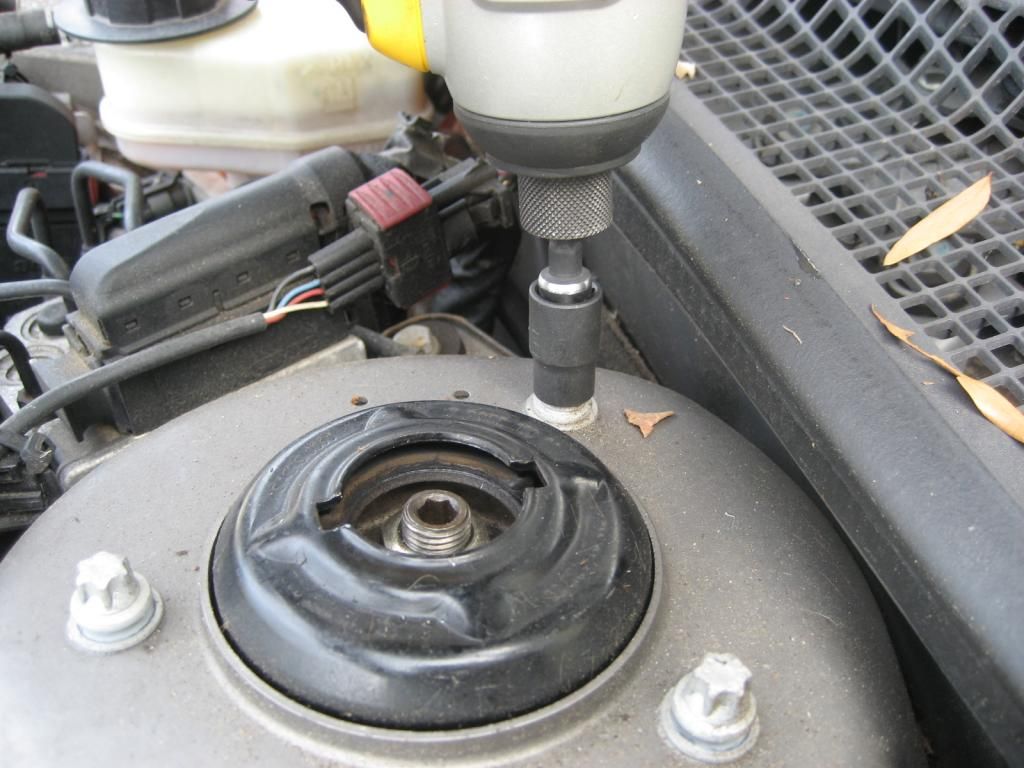
Next, you can separate the strut from the knuckle, and then move it to a convenient spot.

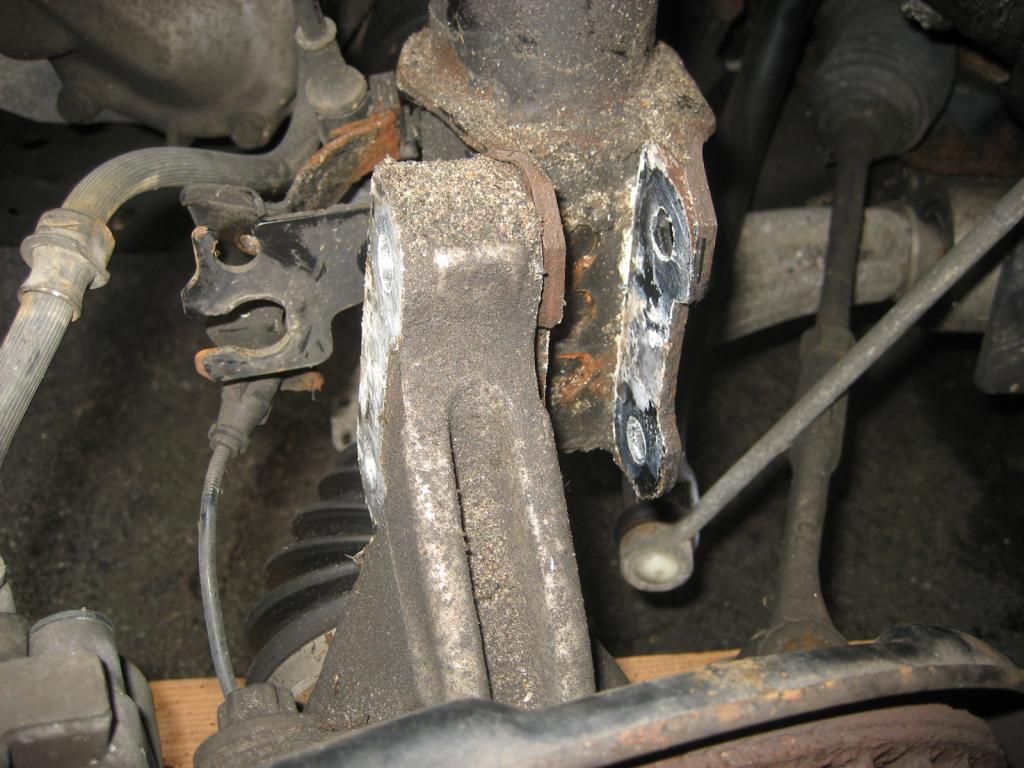
Supporting the strut from the bottom, then remove the final bolt from up top and pull it out.
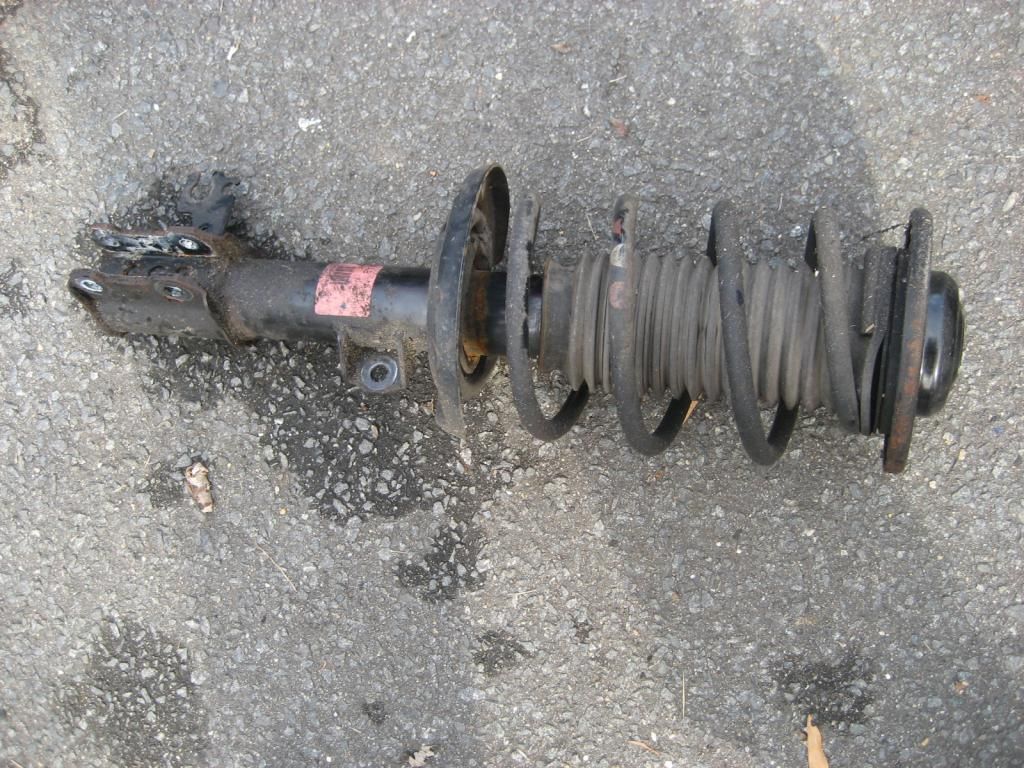
The spring rate is indicated by the color marks on the springs.
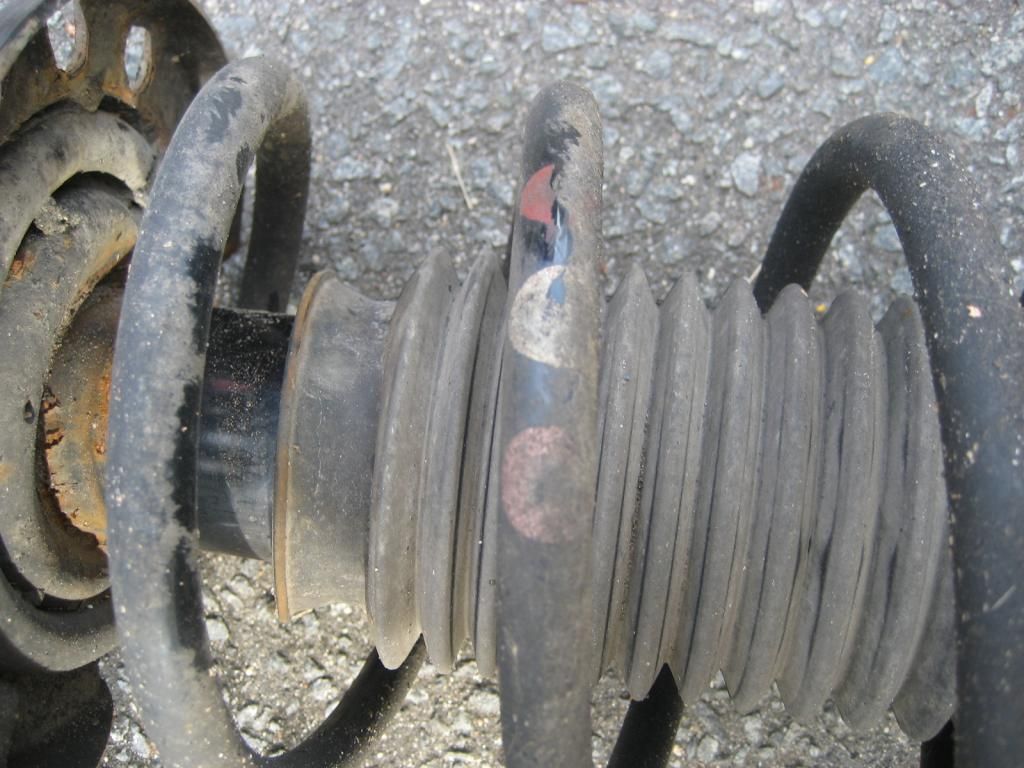