With my leg bothering me and not being able to hobble around I figured that I might as well left foot tig weld for a while to see if I can still fuse two pieces of sixteen gauge mild steel together. Low and behold I can still dip and move a bit, but I need to work on penetration control still.
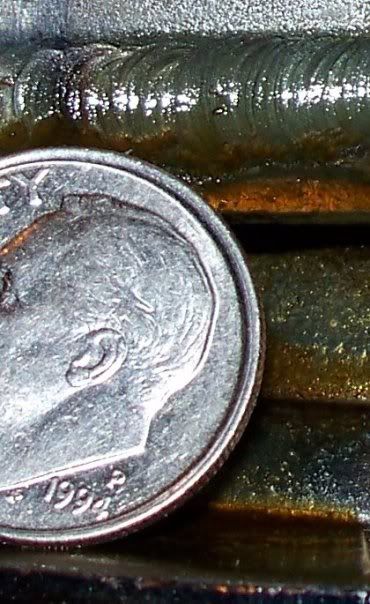