https://www.defense.gov/News/News-S...uel-use-improve-tactical-vehicle-performance/
A prototype for a commercial, hybrid-conversion kit for military tactical vehicles has been designed to reduce fuel consumption, improve performance and decrease logistics demand.
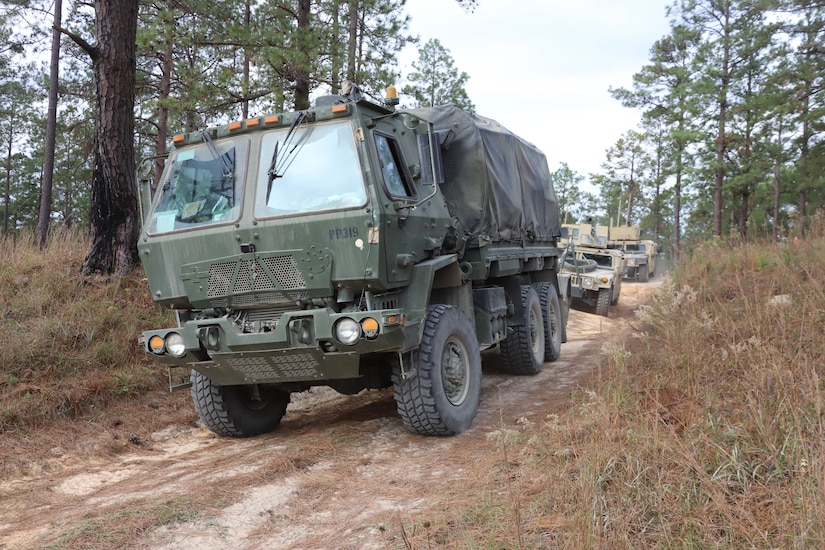
The Defense Department operates a fleet of more than 250,000 tactical vehicles, which frequently operate in austere conditions. These vehicles often spend as much of their operational time stationary as they do in motion, said Ben Richardson, director of the Defense Innovation Unit's advanced energy and materials portfolio.
However, even when stationary, the engines must run in order to power the essential onboard electronics, as well as the heating and cooling systems in the crew compartments. This results in significant fuel consumption while the vehicle idles, he said.
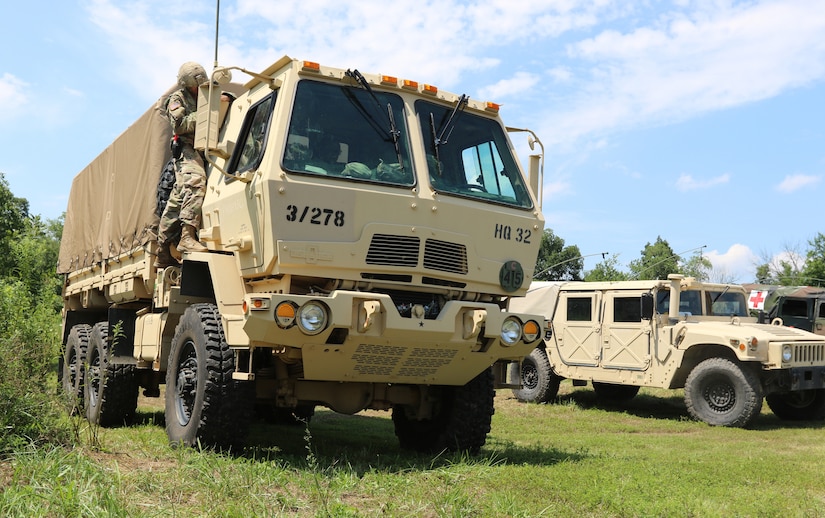
"By integrating an anti-idle capability into our existing fleet of tactical vehicles, the DOD has the opportunity to meaningfully reduce fuel consumption by its operational forces, enabling them to operate longer between refueling," Richardson said. "This also promises to reduce the amount of fuel that must be transported into combat zones, reducing the demand on, and risk to, logistics supply chains.
"This challenge and opportunity are not unique to the military. For years, commercial long-haul, utility, and emergency trucking fleets have been converting their existing trucks into hybrid and full-electric vehicles to save money and reduce emissions."
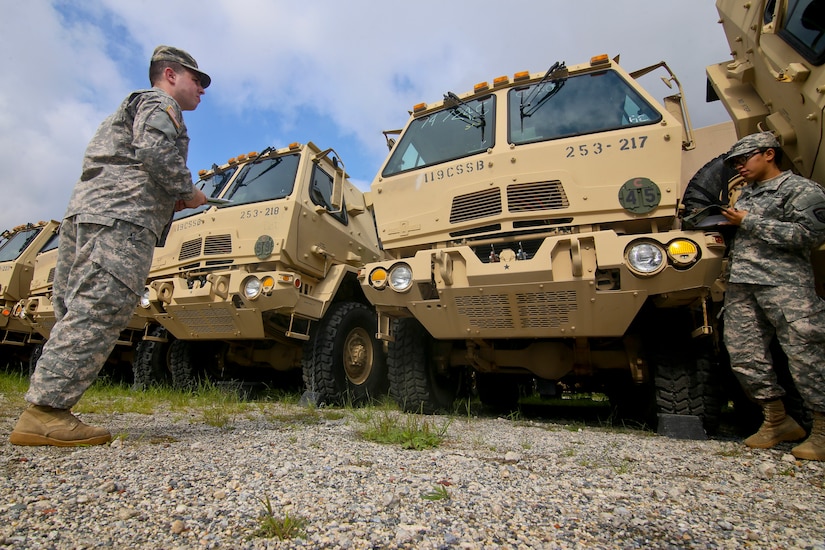
In August, the DIU and the Army's Project Manager Transportation Systems — part of the Program Executive Office for Combat Support and Combat Service Support — issued awards to XL Fleet and Volta Power Systems to integrate their commercial solutions into prototype to idle-reduction some two-and-a-half to 10-ton trucks.
Spotlight: Science & Tech
Idle reduction technologies reduce fuel waste and engine wear.
After demonstration and evaluation of the prototypes, the companies will be asked to develop and deliver a retrofit kit for fielding and easy installation by soldiers operating at logistics depots and motor pools across the force, Richardson said.
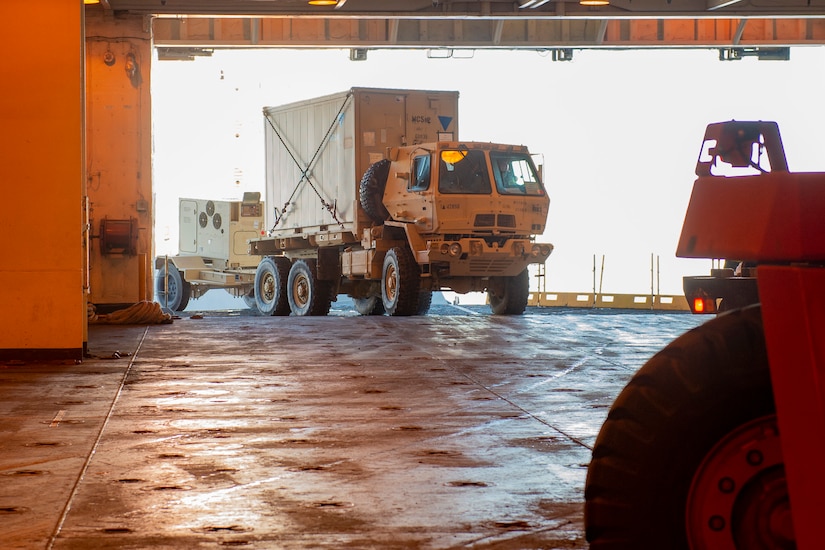
Beyond the fuel savings to be gained from the introduction of anti-idle capability, officials in the Program Executive Office for Combat Support and Combat Service Support also see this as a step toward further hybridization and electrification efforts.
Steve Roberts, the PEO CS&CSS project lead for integration, said collaboration has been key. "The collaboration between DIU and PEO CS&CSS is proving to be invaluable. Their industry connections and contracting flexibilities greatly shortens the time to bring capability to the warfighter. These kits are the first step to a game changer across the tactical, wheeled-vehicle fleet in not only decreasing fuel demand, but also bringing new capability in the form of increased electrical power."
A prototype for a commercial, hybrid-conversion kit for military tactical vehicles has been designed to reduce fuel consumption, improve performance and decrease logistics demand.
The Defense Department operates a fleet of more than 250,000 tactical vehicles, which frequently operate in austere conditions. These vehicles often spend as much of their operational time stationary as they do in motion, said Ben Richardson, director of the Defense Innovation Unit's advanced energy and materials portfolio.
However, even when stationary, the engines must run in order to power the essential onboard electronics, as well as the heating and cooling systems in the crew compartments. This results in significant fuel consumption while the vehicle idles, he said.
"By integrating an anti-idle capability into our existing fleet of tactical vehicles, the DOD has the opportunity to meaningfully reduce fuel consumption by its operational forces, enabling them to operate longer between refueling," Richardson said. "This also promises to reduce the amount of fuel that must be transported into combat zones, reducing the demand on, and risk to, logistics supply chains.
"This challenge and opportunity are not unique to the military. For years, commercial long-haul, utility, and emergency trucking fleets have been converting their existing trucks into hybrid and full-electric vehicles to save money and reduce emissions."
In August, the DIU and the Army's Project Manager Transportation Systems — part of the Program Executive Office for Combat Support and Combat Service Support — issued awards to XL Fleet and Volta Power Systems to integrate their commercial solutions into prototype to idle-reduction some two-and-a-half to 10-ton trucks.
Spotlight: Science & Tech
Idle reduction technologies reduce fuel waste and engine wear.
After demonstration and evaluation of the prototypes, the companies will be asked to develop and deliver a retrofit kit for fielding and easy installation by soldiers operating at logistics depots and motor pools across the force, Richardson said.
Beyond the fuel savings to be gained from the introduction of anti-idle capability, officials in the Program Executive Office for Combat Support and Combat Service Support also see this as a step toward further hybridization and electrification efforts.
Steve Roberts, the PEO CS&CSS project lead for integration, said collaboration has been key. "The collaboration between DIU and PEO CS&CSS is proving to be invaluable. Their industry connections and contracting flexibilities greatly shortens the time to bring capability to the warfighter. These kits are the first step to a game changer across the tactical, wheeled-vehicle fleet in not only decreasing fuel demand, but also bringing new capability in the form of increased electrical power."