With Shannow's photo of a turbine failure in the Industrial section i thought I'd share a couple of pics of a C-130 turbine failure.
This plane landed at Al Ueid AB while I was there in 2003. I pulled the engine off the wing after inspecting it for a write-up of high vibration and shut-down in flight. the crew "saw sparks".
It liberated the rear bearing and rear oil pump somewhere over Saudi Arabia.
This was caused by a rear oil pump failure, which caused the rear bearing to fail, which caused vibration, which caused the struts to fail and the oil pump/bearing assy to fall off, which caused the turbine to fail. it did send parts through the turbine case.
The flight engineer attempted to explain to me how the turbine failed causing the oil pump/rear bearing to liberate, those guys know everything
some specs are:
Allison T-56 engine
13,000 rpm constant
about 24" diameter turbine
about 3500 horsepower
about 1600 lb-ft torque
This plane landed at Al Ueid AB while I was there in 2003. I pulled the engine off the wing after inspecting it for a write-up of high vibration and shut-down in flight. the crew "saw sparks".
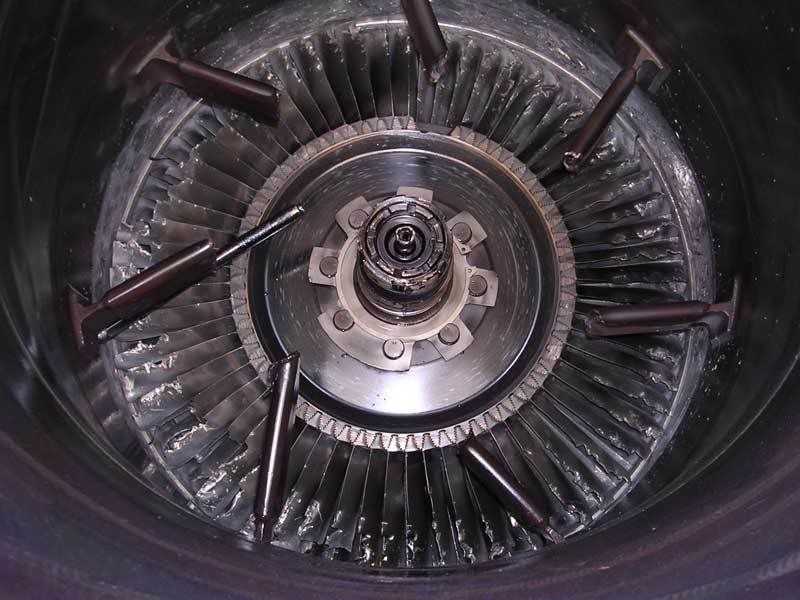
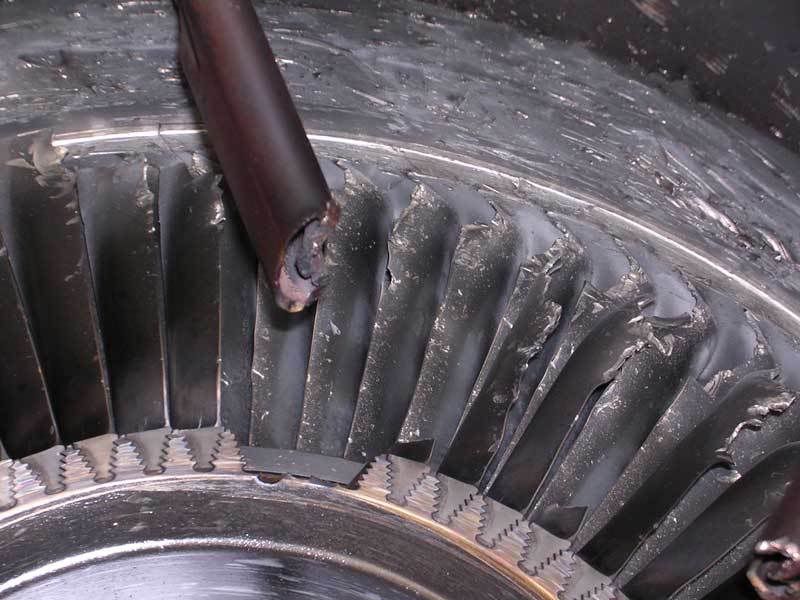
It liberated the rear bearing and rear oil pump somewhere over Saudi Arabia.
This was caused by a rear oil pump failure, which caused the rear bearing to fail, which caused vibration, which caused the struts to fail and the oil pump/bearing assy to fall off, which caused the turbine to fail. it did send parts through the turbine case.
The flight engineer attempted to explain to me how the turbine failed causing the oil pump/rear bearing to liberate, those guys know everything

some specs are:
Allison T-56 engine
13,000 rpm constant
about 24" diameter turbine
about 3500 horsepower
about 1600 lb-ft torque